Introduction#
Overview of Palletizing Workstation System#
The DUCO PalletStudio palletizing workstation is an integrated hardware and software solution for box stacking applications that includes DUCO’s high payload collaborative robot GCR25, a palletizing base and a software package for control. Compared to traditional industrial robotic arms, the collaborative robotic arms form a palletizing workstation with a smaller footprint, higher safety, electronic safety fencing supplemented by collision detection of the collaborative robots, and no need for additional fencing for protection, making it more agile. This brochure helps customers to understand this palletizing workstation and provides information on how to set up and activate your palletizing configuration.
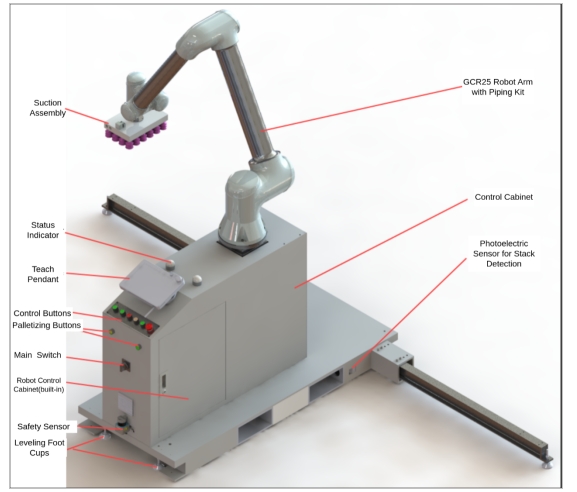
Figure 3.1 Schematic diagram of the palletizing workstation (front)
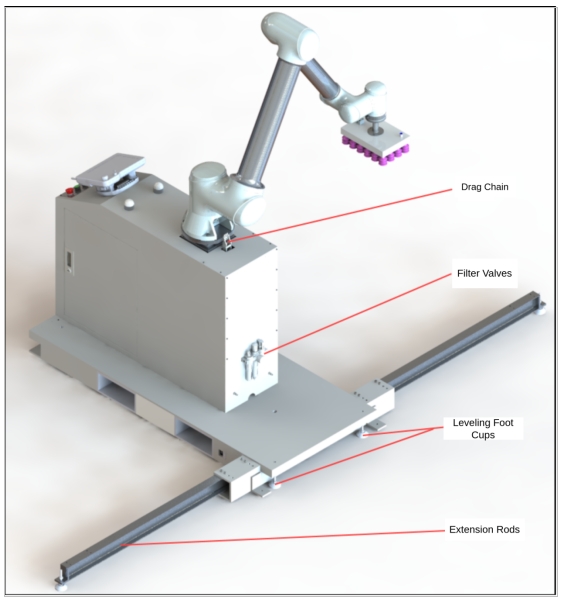
Figure 3.2 Schematic diagram of the palletizing workstation (back)
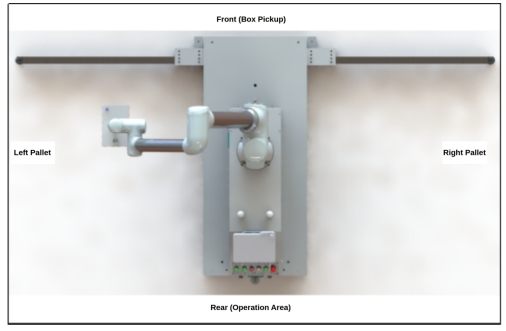
Figure 3.3 Top view of palletizing workstation
Introduction to Palletizing Workstations#
The palletizing workstation consists of the DUCO-GCR25 collaborative robot, the electrical control cabinet (including the robot controller DC30D-J9), the portable mobile base and pallet positioning system, and the palletizing control system. The overall palletizing workstation can be fully controlled by our control cabinet.
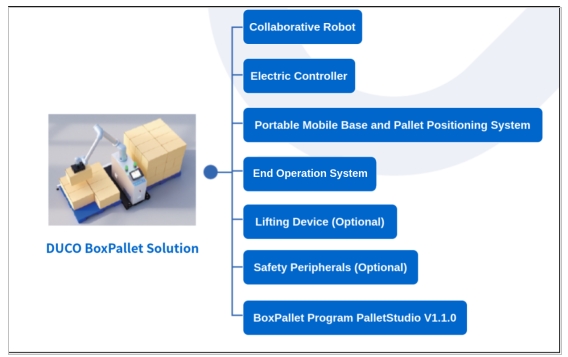
Figure 3.4 Schematic diagram of the components of the Code Multi workstation
1 DUCO-GCR25 Collaborative Robot
The collaborative robotics system consists of the following main components:
Robot
Robot control cabinet
Connection cable
Software
Other options, accessories
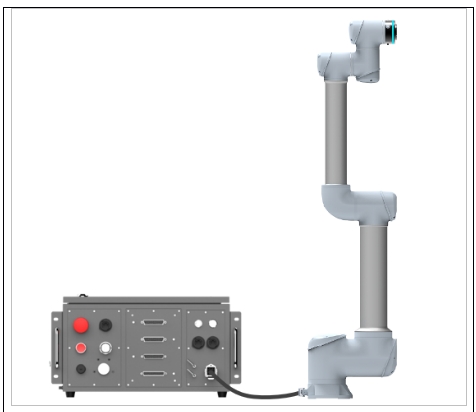
Figure 3.5 Overview of the robot system
System Parameters |
|
---|---|
Degrees of freedom: 6 |
Load (TCP): 25kg |
Workspace: 1800mm |
Repeat positioning accuracy:±0.05mm |
Working Temperature: -10~45 |
IP rating: IP54 |
Installation: Floor-mounted |
2 Pneumatic suction assembly
a Air tube: Including two φ8 air tubes for inlet and outlet, the outlet is used to create negative pressure, and the inlet is used to release items.
b Suction devce (including negative pressure sensors): used to suck up palletized items, the sensor will output a high level signal after reaching a certain negative pressure threshold.
c Robot Tubing Kit: The robot tubing kit is designed to hold the cables for the air tubes and negative pressure sensors along the arm so that they do not get tangled in the arm during suction cup rotation to cause risks such as the air tubes falling out.
3 Lifting column (or fixed column): controls the raising and lowering of the robot arm, determines the number of layers that can be palletized, and includes the drive and motor.
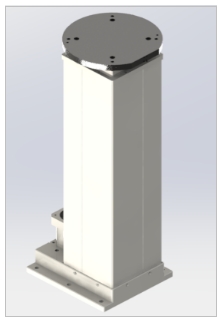
Figure 3.6 Schematic diagram of the lifting column
4 Control cabinet components
a DC30D-J9 Controller: The GCR25 is equipped with a controller capable of controlling all the tasks of the overall palletizing station, in the form of a modular workstation in the form of a control cabinet, for rapid deployment and maintenance.
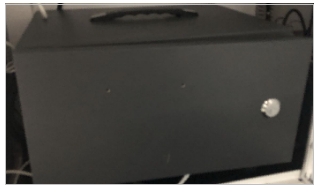
Figure 3.7 DC30D-J9 controller
b Circuit breaker: Circuit breakers can be used to protect circuits and equipment from damage caused by overloads, short circuits and other faults, and to ensure the safe operation of circuits. They can also be used to switch circuits and control the start, stop and operation of various electrical equipment.
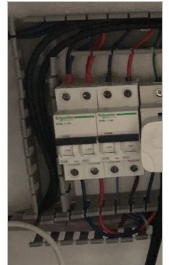
Figure 3.8 Circuit breaker
c On-off switch: Controls the up and down power of the whole station. The white arrow pointing horizontally to the left to O means the circuit is closed, and turning the switch to the right by 90° to point to I will turn on the circuit.
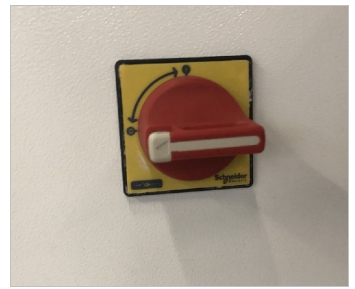
Figure 3.9 On-off switch
d Safety sensors (optional) for setting up safety zones: used to ensure that the machine stops when there is a person or foreign object in the designated area, and also to monitor that the robot stops when a person enters the robot’s work area.
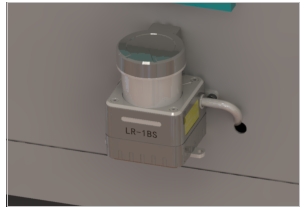
Figure 3.10 Safety sensors
e Three-color light with buzzer: Provide present status indication, warning to remind the current status.
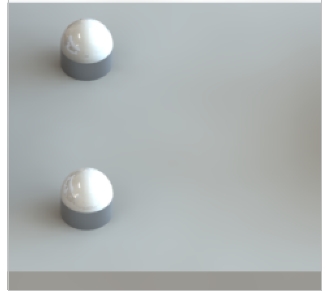
Figure 3.11 Three-color light with buzzer
f Drag chains: Regulate the movement of air hoses and robot cables with the lifting column to avoid entanglement and abrasion.
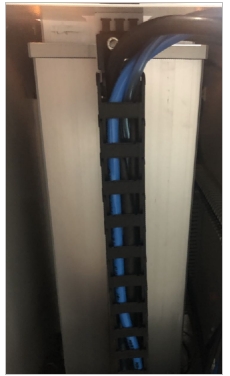
Figure 3.12 Drag chain
g Buttons: physical buttons that control the palletizing workstation, with the specific functions shown in the figure
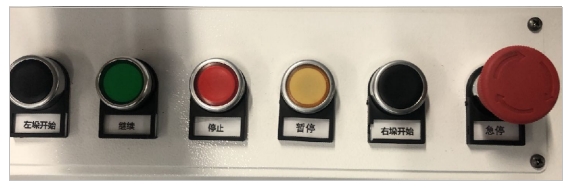
Figure 3.13 Buttons
Palletizing Workstation Specifications#
Model number |
DUCO-PS-0-0 |
DUCO-PS-80-1 |
Working radius |
1800 mm |
|
Maximum pallet size |
1200×1200 |
|
Maximum height |
1700 mm(Fixed base) |
2500 mm(Lifting base) |
Height of lifting column |
not have |
850 mm |
Maximum lifting height |
not have |
800 mm |
Palletizing speed packages
|
6-8 boxes min |
|
Repeat Positioning Accuracy |
±0.05 |
|
Communication method |
TCP IP |
|
IP Class |
IP54 |
|
Temperature range |
0~55 |
|
Rated power |
1.5 kW |
|
Power supply (of an appliance etc) |
100~220 AC |
|
Weight |
522 kg |
472 kg |
Area |
3320×1665(including extension rod) |